Just How Specialist Product Packaging Device Repair Service Solutions Lessen Downtime and Increase Performance
Specialist packaging device repair services are important in reducing downtime and enhancing productivity via specialized diagnostics and timely treatments. The ramifications of such services expand past prompt repair work-- unboxing the wider effect on functional effectiveness exposes critical understandings into long-lasting performance approaches - packaging machine repair service.
Relevance of Timely Repairs
Timely fixings of packaging equipments are vital for maintaining functional performance in any type of manufacturing environment. When machinery breakdowns or breaks down, it can result in significant interruptions in manufacturing lines, leading to raised downtime and lost earnings. The longer a packaging machine stays out of order, the greater the effect on total efficiency, possibly creating delays in meeting orders and reducing customer contentment.
In addition to the prompt economic effects, postponed repairs can lead to more extensive damages to the equipment. Elements that are not dealt with promptly can weaken even more, calling for more pricey repair services or total replacements, which could have been stayed clear of via timely intervention. In addition, regular upkeep and punctual repair services can enhance the lifespan of product packaging equipments, guaranteeing that they operate at optimal efficiency levels.
Purchasing expert packaging machine repair solutions is necessary for mitigating these threats. A proactive strategy to repair services not just maintains production timetables but also fosters a culture of reliability within the organization. By focusing on prompt fixings, businesses can maintain their affordable side, optimize resource allowance, and eventually boost their bottom line through boosted functional performance.
Experience in Diagnostics
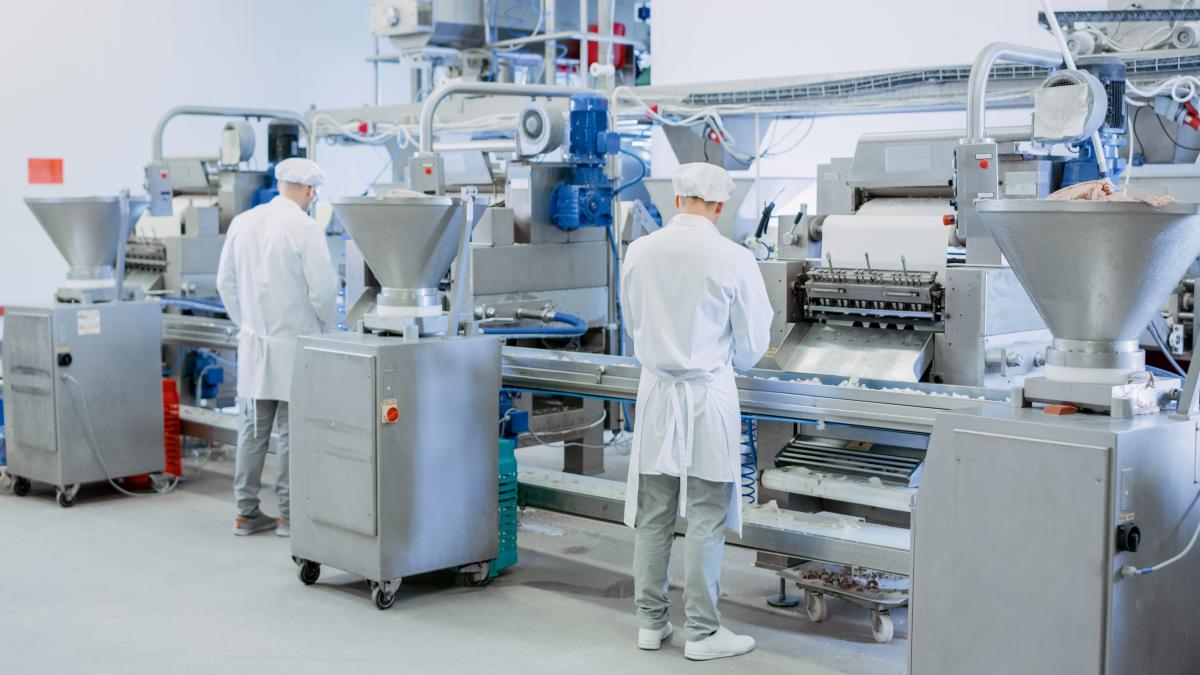
Efficient diagnostics not just facilitate quick identification of issues however also enhance the overall reliability of packaging procedures. By carrying out thorough evaluations, service technicians can examine the wellness of important elements, ensuring that also minor irregularities are dealt with quickly. This attention to information lessens the threat of unexpected break downs, which can result in costly downtime.
Additionally, specialist diagnostics supply valuable understandings right into functional trends, enabling organizations to make enlightened decisions pertaining to devices upgrades or modifications. By leveraging these understandings, companies can maximize their product packaging procedures, leading to improved effectiveness and performance. Ultimately, buying analysis proficiency is crucial for companies looking for to maintain smooth procedures and promote high standards of quality in their product packaging processes.
Preventive Maintenance Advantages
Precautionary upkeep enhances expert diagnostics by proactively addressing like this potential issues prior to they show up right into significant issues. By executing a structured precautionary upkeep program, firms can significantly reduce the threat of unanticipated maker failures, thus reducing expensive downtime. Normal evaluations, cleansing, and parts substitute help make sure that product packaging machinery operates at ideal performance.
One of the crucial benefits of preventative maintenance is its capacity to prolong the life-span of equipment. By routinely keeping machinery, businesses can avoid the worsening effects of deterioration that frequently bring about significant repairs or substitutes. packaging machine repair service. This not only saves funding but likewise enhances the total integrity of production procedures
Furthermore, preventative maintenance adds to boosted safety and security problems within the workplace. By determining and remedying prospective threats prior to they escalate, organizations produce a more secure setting for their workers. This aggressive approach not only secures employees yet also fosters a society of responsibility and caution.

Customized Solution Solutions
Acknowledging the unique needs of each service, personalized service solutions for product packaging machine repair offer customized techniques that boost operational effectiveness. These solutions are made to resolve specific challenges faced by different markets, making sure that machine downtime is reduced and productivity is maximized.
Expert repair work solutions start with a comprehensive evaluation of a firm's packaging operations. By understanding the details machinery involved and the needs of the manufacturing environment, specialists can create a personalized repair and maintenance strategy. This may consist of specialized training for in-house team, the application of predictive upkeep innovations, or the arrangement of dedicated support during peak production times.
Moreover, personalized options can incorporate versatile solution arrangements that align with a company's operational timetable, enabling repair services to be done during off-peak hours. By prioritizing the distinct requirements of each company, these custom options ensure that repair services are not only reliable yet likewise seamlessly incorporate into existing workflows.
Ultimately, the emphasis on modification allows companies to maximize their packaging processes, leading to enhanced reliability and performance of equipment, which is essential for keeping competitive advantage in today's fast-paced market.

Effect On Overall Efficiency
Personalized solution options not just try this address particular repair service demands however likewise play a substantial duty in enhancing overall functional performance. By supplying targeted interventions, specialist product packaging equipment repair service services straight decrease the regularity and period of devices failings. This proactive approach ensures that assembly line stay operational, reducing disturbances that can lead to expensive downtime.
Additionally, efficient repair services contribute to smoother process, as well-kept equipment operates at optimal efficiency degrees. When machines work appropriately, the top quality of packaged products improves, bring about less problems and less rework. This enhancement not only improves performance however likewise enhances client contentment.
On top of that, regular upkeep and quick action times from repair service specialists cultivate a culture of dependability within the company. Workers can focus on their main tasks instead of bothering with prospective devices malfunctions. Subsequently, the general throughput of the manufacturing process boosts, enabling companies to meet need better.
Inevitably, the strategic investment in expert repair service services equates to enhanced efficiency throughout all operational facets, making sure that organizations can adapt and flourish in an open market. This synergy between maintenance and performance is vital for long-term success.
Final Thought
To conclude, specialist product packaging device fixing solutions play a crucial function in decreasing downtime and improving efficiency within producing atmospheres. Timely repair work, expert diagnostics, and preventative maintenance add to the integrity click over here now of devices, while customized solution options address particular functional demands. The advancing effect of these services causes improved overall efficiency, enabling services to maintain production timetables, copyright product top quality, and properly fulfill market demands. Buying such services ultimately drives sustained functional success.
Comments on “Packaging machine repair service with certified technicians you can rely on.”